The 101 on Compound Turbo Systems: Our FAQs Answered
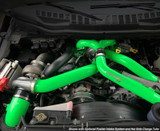
Why is a single turbocharger not good enough?
A single turbo is a very simple and effective way to make good power, but (and this is a big but), they can only cover a given range of power effectively. The factory turbos on most light duty diesels are typically small, giving the trucks great throttle response. Aftermarket single turbos are often bigger, giving the trucks great top-end power. But ask the small turbo to give you top-end power, or ask the large turbo to give you great throttle response, and you’ll be left with lackluster performance. Each has their pros and cons, and that’s where the beauty of running these two sizes together makes itself clear.
What are compounds / how do they work?
These highly popular systems make incredible efficiency and power by combining two turbochargers, in which one turbocharger feeds the other to create double the intake pressure (commonly referred to as boost). In these systems there is a primary (small) high pressure turbo and a secondary (big) atmospheric turbo: the primary turbo receives the exhaust flow first, and given its lightweight and smaller nature, it quickly powers low engine RPM boost. Continuing on its way, the exhaust leaving the primary turbo is routed over to the secondary turbo. But where the magic starts to happen is once the primary turbo begins to reach its maximum desired RPM – that’s when the vanes / waste gate open, bypassing exhaust around its turbine wheel and directly into the secondary turbo effectively ‘handing over the baton’ so your engine can continue to easily create boost in the mid-to-upper engine RPMs.
On the intake side of things, people are generally surprised to find the flow is opposite of what they suspect. The secondary turbo sucks air from the atmosphere (hence its name) and pressurizes it, then feeds it to the primary turbo which pressurizes it further.
A compound turbo system is sometimes incorrectly referred to as “twins”. Twins are turbos in parallel with each other; they operate independently of each other. They are generally used on V-type engines where each turbo is fed exhaust by its respective bank, and the charge air from each turbo is then fed into the same area (intercooler then engine). This is a single stage system (whereas a compound system is considered two-stage).
A simple analogy when comparing these two different types of systems is to consider batteries. When you connect two batteries together in a series they make twice the voltage, which can be equated to pressure in a compound turbo system. On the contrary, when you connect two batteries in parallel they create twice the amperage, which would be equated to your flow rate on a twin turbocharger system.
Ultimately both systems achieve the same result, but their platform application is very different. Twins are often used on gas-powered engines because they can turn about twice the RPM a diesel can. The only way to generate the same power output in a diesel is to increase the pressure of the air delivery.
Aren't compounds for race trucks?
Surprising to many, compound systems have been around for quite some time in many different OEM forms (consider the 6.4L Powerstrokes, which came with factory compounds). However, their initial rise in the diesel community’s awareness primarily came from the early days of light duty diesels becoming a popular competition platform, which led many people to make the assumption that only highly modified “race” trucks would dabble in compound systems. But consider the benefits of a compound turbo system: greater efficiency, reliable power through all RPM levels, considerably lower and stabilized EGT temps – these are benefits that lend themselves to all owners (especially for towing - where efficiency, power and EGTs suffer the most).
Ironically, the race opinion has been shifting away from compounds toward a single big turbo combined with a shot of nitrous as the way to go in the drag race and dyno applications; there are so many more options available now that the broad power and benefits of compounds for racing can be replaced with finer tuned and purposefully designed big racing singles.
Why not just upgrade my factory turbo?
There are a ton of options for upgrading a factory turbo, and I could spend all day talking about them. But at the end of the day, no single turbo can provide the same power curve that two turbos can. I’ll use the 2nd gen swaps on the Cummins for an example: You can put something like a 66mm S300 or S400 on a Cummins and make in the 650HP range easily but your low-end performance and vitals while towing are not anywhere near to what a compound system can offer.
Additionally, there is always a considerable amount of waste energy leaving a single turbo (regardless of its size) that can be harvested by placing another turbo behind it, to help convert that exhaust energy back into boost, but that’s a topic for another day.
Won’t compounding my factory turbo blow it up?
No, and in fact I believe compounds are a safeguard for your factory turbocharger. Consider a scenario where a turbocharger might “blow up” – such as if you’re towing a heavy trailer on the highway. If you are running just your factory charger (or any appropriately sized single) it will be working overtime to move the air you need to make the power necessary to travel at the same speed. You’d already be past where that charger is efficient, and as a result not only is that single turbo living a less than ideal life, your engine is seeing higher EGTs and drive pressures. When you add an appropriately sized larger charger into the system you share the work load, effectively dropping the rpm of the small turbo down to where it is efficient – back to its happy (and safe) place. The same goes for racing or competition scenarios. When it comes to getting a job done – two is better than one.
Will compounds make my truck unreliable?
A compound system will not make your truck less reliable – but by adding them to your truck you’ve unlocked a whole lot of additional potential. Our base compound systems provide enough air for 700-750hp. If you decide to tackle that potential and add additional mods (fuel, injectors, etc) then it’s important to note that 700hp and 500hp are not the same thing. More power is more load and wear on parts, period. Setting up your truck the right way will minimize accelerated wear, but as a rule of thumb: more power wears parts faster. You can’t expect to play at 700hp all the time and get the same life out of your drivetrain that you would at 500hp.
But again, it’s not the compounds that are increasing that potential wear. Your truck is going to be a whole lot safer and more reliable at the 500hp mark and below with compounds than it is trying to make that same power with the factory charger.
Do I need custom tuning?
Yes, but nothing too crazy. Tuning mainly comes down to what you have on the truck already, or plan to add at the same time. If you’re just bolting on compounds on an older truck with a fixed geometry turbo, the only change you’ll need to make is to set your waste gate to open sooner, which we cover in our instruction manuals. On the newer trucks equipped with a MAF sensor and variable geometry turbos, you will have to setup the MAF for our larger cold air intake and have the vanes open earlier, but that’s pretty simple stuff that is also covered in our instructions.
How involved is the installation?
Our systems are very straightforward, and come with 15-plus pages of color instructions with pictures. They have all been designed to be installed in the driveway, and with intermediate prior experience you can expect an install time of 6-8 hours, more or less.
I feel we walk the line of performance and fitment really well, and we place a high value on system longevity. I design everything as if I was going to have it on a vehicle for the long term, but with the flexibility to potentially move the compound system to another truck at some point. We spend a considerable amount of resources in designing our systems to ensure the least impact possible on surrounding components in the engine, without compromising the performance of the system or ease of installation. And that dedication results in engine bays that are more open, and easier to work on in general, post installation.
A great example here is our new compound system for the 6.7L Fords - we looked hard at keeping the factory sized passenger side battery in the engine compartment with the additional turbo, but at the end of the day there was no way I would want to own a truck with all of those components just crammed in there. So we put the atmospheric where it was best suited for routing, and then from there figured out what had to be done to accommodate that. As a result, prioritizing that routing required a smaller, higher performing battery and a new low pressure AC line – both of which raised the cost of the system. But now have the only system that fits easily into those models, and routes optimally in the engine bay. No rubbing parts, significantly easier to install and way easier to maintain. A small price to pay for such a big difference.
The same thing goes for our Duramax specific systems, keeping the factory battery and coolant reservoir under the hood is just too tight. Fortunately the trucks have enough battery cable in the harness to reach where the passenger side battery is located on the frame rail like the vans. So we’re able to supply to OEM battery tray that the vans use so you have a factory like setup there, and then we supply a new all aluminum coolant reservoir which is lower profile and mounts where the battery was. With that done the engine bay is so much more open, and so much easier to work on.
How much does a compound system cost?
The cost really can vary depending on turbo setup and vehicle. Our complete Cummins specific systems are in the low $3,000 range, the Duramax systems are in the low $4,000 range and the new Powerstroke system should be right at $5,000. So for me when you’re looking at a turbo upgrade and an upgraded single turbo with a good track record is in the $2,000 range, and a single turbo system like a 2nd gen swap for a Cummins is in the $3,000 range - it’s really hard to justify them over compounds considering the massive differences in performance and benefits.
What are the hard numbers on performance improvements?
The light duty trucks that we focus on are all equipped with very similar hardware. The engine displacements are all very close, the factory turbos are all very close in size. So when we put just our base compound system on we generally see an 18-23% improvement in EGT’s and MPG’s - and the harder you run the truck, the higher the those improvement numbers rise.
What are some major don'ts to look out for in a compound system design?
As a customer, you should carefully analyze every aspect of the system.
- How is the atmospheric supported / bolted onto the engine? This is going to directly affect the durability of the system. We’ve sold a lot of systems to customers that unfortunately bought a system with an inadequately mounted (or not mounted at all) atmospheric turbo and the system fails pretty quickly.
- Where is the atmospheric turbo placed? This is going to dictate how the rest of the system is designed, and how hard it is to install.
- Are irreversible modifications to the surrounding engine bay components necessary?
- Will it be easier, or more difficult to work on the truck after installation?
- How is the system made? Is it made on a mockup engine or in dedicated weld fixtures? There are a lot of kits out there made in a “one-off manner” which means their fitment can very greatly from one to the next.
- How is the oil drain configured? The later model Cummins trucks have an auxiliary oil drain port right on the side of the turbo side of the block which is awesome for returning oil from the atmospheric turbo. The Duramax and Powerstrokes are not so easy. You should look into what is involved with plumbing return oil back in, and where it’s going when it gets there. Is it above or below the oil line in the pan?
- How unique are the components supplied in the system? If you have a silicone coupler fail, is it a relatively standard size/shape or can you only get it from the manufacturer of the compound system? What if they stop making that design or are on back order?
- What is the quality level of the small components provided? Are the clamps all stainless? Are the hoses, bolts, gaskets, etc up to par and from reputable manufactures?
- Are instructions and hardware included? (You would think it would be a resounding yes across the board, but it’s not).
The bottom line is there are a lot of ways to design compound system, and a lot of options to consider. I encourage you to do the research and educate yourself on each system you think fits your needs.